RDF Gasification
Production of Refuse Derived Fuel (RDF) should always be part of Municipal Solid Waste (MSW) handling. The RDF process recycles valuable resources and is profitable. The RDF is homogenous and may be used as raw material to Gasification Processes.
The production of RDF from MSW has been used for decades. The process is capable to separate, automatic or manual, the incoming waste into several fractions like plastic, wood, iron, other metals etc. The volume reduction is normally around 50 %. 50 000 tpy MSW may be divided into 25 000 tpy recycled material and 25 000 tpy RDF including inerts that will be stored on the waste filling. Treating RDF the right way by partial drying and torrefaction will enable storing and different usage. RDF is a homogenous fraction of the MSW containing organic substances with high calorific value. This fact makes it perfect for gasification and production of different forms of energy.
Process Items
RDF Plant
- Pre-shredder
- Ferrous Separator
- Waste screen/Wind-sifter
- Re-shredder
- Storage Silo
- Loading and Un-loading system
- Eddie Current Separator
- Flip Flop Screen
- Filter System
Gasification Plant
- Inlet hopper
- Dryer
- Gasifier
- Heat exchanger
- Filters
RDF Plant Specifications | |
---|---|
MSW amount | 50 000 tpy |
Gate Fee | € 25 /ton |
Electricity | € 0,15 /kWh |
Revenue | € 6,3 million |
Profit | € 5,3 million |
Company Profile
ScandGreen Energy design, develop and build portable, modular and scalable waste-to-energy solutions. We utilize proprietary technology to transform low-value biomass and waste into renewable energy, while detoxifying emissions, hazardous compounds and reducing greenhouse gases. Applications include Land Remediation, waste management and renewable energy.
The advantage of Bio-Reforming and GTL is that the use of syngas is potentially more efficient than direct combustion. Syngas may be used directly as a fuel in internal combustion engines, fuel cells, used to produce hydrogen, or converted via catalytic processes into synthetic fuel.
Refuse Derived Fuel
Appropriate RDF production process consists of manual sorting, magnetic separation, bag breaking/homogenization, screening with the opening of 40 mm, air drying, shredding and palletizing. This process can produce RDF that has average lower heating value (LHV) around 12–20 MJ/kg at 10–15 % moisture content. Chlorine and sulfur contents are usually lower than 1 %. Heavy metals such as Cd, Cr, Hg and Pb do not exceed European RDF standard.
A definition defined by ASTM
standard (
MSW composition is varied from different sources, seasons and living behaviors. Raw MSW has high moisture content, low calorific value, wide range of particle size distribution and high ash content. These reasons make using raw MSW as fuel difficult and unattractive. RDF presents several advantages as a fuel over raw MSW. The main advantages are higher calorific value which also remains fairly constant, more uniformity of physical and chemical composition, ease of storage, handling and transportation, lower pollutant emissions and reduction of excess air requirement during combustion.
Quality assurance in the production of RDF requires that RDF should have high calorific value and have low concentration of toxic chemicals especially for heavy metals and chlorine. Although the RDF quality regulation varies in different regions. We can follow European standard as a guideline and develop our own standard according to local situation later on.
Usage of RDF
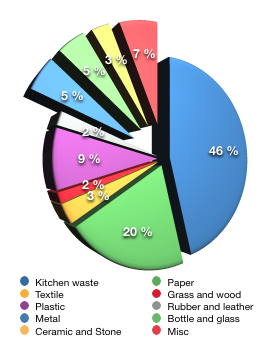
Typical waste composition.
RDF production process has two subsystems called front end and back end. Front end or pre-processing subsystem is to receive the MSW and separate it into combustible and noncombustible fractions in order to produce feed stock for back end system. Back end system refers to the conversion process which can be either thermal or biological system.
RDF production line consists of several unit operations in series in order to separate unwanted components and condition the combustible matter to obtain required RDF characteristics. General unit operations are screening, shredding, size reduction, classification, separation either metal, glass or wet organic materials, drying and densification. These unit operations can be arranged in different sequences depending on coming MSW composition and required RDF quality.
The term “size reduction” in solid waste management is similar to “shredding” and “grinding”. But the term “shredding” often refers to size reduction of the mixed wastes. The term “grinding” is sometimes used for glass. Size reduction is an essential unit operation in mechanical processing of mixed wastes since it gives a certain degree of size uniformity. Shredding of mixed waste to the size of about 10 cm. is common in many waste processing facilities. Sometimes, secondary or tertiary shredding to the size of smaller than 10 cm. is required for production of RDF.
Production of RDF is in almost all cases economic and will reduce the amount of MSW with 50 % which means less land fillings. However, RDF is too valuable just to be stored and disintegrated.
We recommend using RDF as a raw material for the production of electricity and heat by gasification. Different gasifiers and filters may be used depending on front-end treatment and composition.
The syngas from the gasifier could also be used to produce liquid fuels through our patent pending Gas-to-Liquid fuel unit (GTL). Typical end products are diesel, gasoline, kerosene and jet-fuel according to ASTM standards. This functionality could be added at a later stage (we refer to our GTL information memo).
Compared to incineration of RDF, gasification can double the amount of electricity exported to the grid, thus eliminating the hazardous emissions and most of the residues. Gasification will not produce furans, dioxins or NOx. The ashes from gasification may be used as soil improvement, while incineration produce toxic ashes up to 10 times the weight.
Incineration can not be used for other purposes. Syngas from gasification can be used for several purposes as described above. In addition several other products may be produced like fertilizer, specialty chemicals, plastic etc.
Combining recycling with power production (PP) means making the most out of everything. It also involves a lot of evaluation of local market demand and has to be done carefully to optimize the output. With our expert knowledge in gasification and emission control we have specialized in this field and will assist you in a complete feasibility study for your special demands and requirements.
Below we have compiled a typical RDF-PP case that optimize the overall output.
RDF Gasification
Download a PDF file of RDF gasification.